Clean rooms are critical in many conversion and manufacturing processes because they ensure strict production of high-quality, contaminant-free products. Certified clean rooms incorporate advanced air filtration and other contamination control measures to minimize pollutants that negatively affect the final product. The room’s controlled environment maintains consistent and precise manufacturing conditions vital for applications where even microscopic particles cause significant issues.
Clean Room Manufacturing Basics
For many sensitive manufacturing or conversion applications, businesses must realize the importance of clean room manufacturing because it directly impacts finished product quality, performance and reliability. Understanding the basics enables operating a facility that maintains strict cleanliness standards to prevent contamination during production.
What Is Clean Room Manufacturing?
A clean room is a specially engineered space that maintains a low concentration of airborne particles. Clean rooms require strict procedures before entry and specific protocols that curtail the introduction of contaminants like chemical vapors, dust and aerosols.
Even the smallest particles can cause product defects and problems for consumers later in the product’s life cycle. Clean rooms are critical for top-quality output in product manufacturing and conversion across various applications, including medical, aerospace, electronics and semiconductors.
The Role of Air Filtration and Contamination Control in Clean Rooms
A highly functional air filtration system is among the most critical elements of an effective clean room. Ultra-low particulate air (ULPA) and high-efficiency particulate air (HEPA) filters are some required solutions that maintain a clean working environment.
Choosing specific filter types depends on a clean room’s classifications and the industries it serves. Secondary factors like airflow rate, energy consumption and the particles requiring filtering also determine an air filtration system’s unique design.
The Importance of Clean Room Certification and Compliance
Clean room certification and compliance are essential because they assure manufacturers and customers that the work area operates consistently within specified parameters and industry standards. Certification typically involves a third-party assessment evaluating the design, construction, operating procedures and maintenance practices. Certifications such as ISO 7/Class 10,000 and ISO 8/Class 100,000 ensure the clean room meets specific cleanliness requirements based on particle concentration levels.
Clean Room Working Conditions and Responsibilities
Many clean rooms require controlled access points with features like airlocks and interlocking doors that prevent uncontrolled airflow and limit contaminant entry. A room’s design also reduces contamination by utilizing floors, walls, work tables and equipment with smooth, sealed surfaces. Monitoring environmental factors like particle count, air pressure and temperature detects deviations and maintains optimal manufacturing conditions.
Additionally, clean rooms must undergo strict cleaning procedures to remove potential contaminants from surfaces and equipment, including approved cleaning agents and methods for specific equipment and applications.
Innovations in Clean Room Manufacturing
With a rising demand for clean room manufacturing across industrial applications, the need for innovative and technologically advanced solutions grows. Manufacturers and converters that implement the most effective contamination control systems can ensure their finished products exceed the minimal certification standards.
Technological Advancements in Clean Room Manufacturing
Sophisticated air filtration systems with higher particle-capturing efficiency and lower energy consumption have recently emerged across the industry, improving air quality and minimizing contamination risks. Specialized materials and surfaces with antimicrobial properties, electrostatic discharge (ESD) control and improved cleanability also reduce contamination risks and promote cleanliness. Automated systems and robots minimize human intervention and pollutant risk by performing material handling, assembly and quality control functions.
Future Trends Shaping Clean Room Manufacturing
Manufacturers must embrace rapidly evolving technology to exceed the competition. Companies are adopting Industry 4.0 concepts, incorporating automation, data analytics, artificial intelligence and Internet of Things (IoT) technologies to optimize processes, monitor performance and enhance efficiency.
There is also growing emphasis on developing clean rooms with sustainable design practices and energy-efficient technologies, including using renewable energy to optimize airflow systems, decrease operational costs and reduce environmental impact.
How Advantage Converting Can Help
With decades of industry knowledge and experience, Advantage Converting can accommodate your clean room manufacturing needs. Our state-of-the-art Bay Area facility features clean rooms that handle various conversion applications, including custom die cutting, laminating, and slitting and rewinding. As a 3M Preferred Converter, we are recognized for having the expertise to exceed manufacturing expectations in innovation and quality.
Contact us to discover how our capabilities can benefit your business.
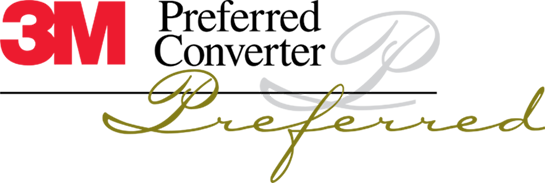