
Case Study
Electric Vehicle Manufacturer Maintains Production and Obtains a Zero-Failure Rate with the Help of Advantage Converting
Challenge
A leading EV manufacturer was awaiting the arrival of a custom built machine designed to laminate insulation material around cooling tubes for battery temperature control in its vehicles. The machine, built overseas, was delayed by 12 months. In the meantime, to maintain its supply of EVs, the company sought a manufacturing partner to develop a method for laminating the material and to maintain production pending the arrival of the equipment.
Solution
Advantage Converting created custom tooling to heat, fold, and wrap a thin insulation film around 20-foot-long aluminum cooling tubes. We built a custom thermal lamination fixture on our existing lamination equipment that provided a consistent encapsulation around the cooling tubes. To address the difficulty of obtaining a consistent bond, Advantage Converting plasma-treated the insulation film prior to lamination. This process increased the strength of the material bond and resulted in zero voids, ensuring a successful product.
Advantage Converting then pot tested, palletized, and shipped the finished tubes to various manufacturing plants where they were formed into giant serpentine patterns.
Results
- Working closely with the EV manufacturer’s engineering team, Advantage Converting applied decades of experience to develop an innovative solution to a unique problem
- Plasma-treating the film resulted in a zero-failure rate, which reduced the scrap rate, improved yields, and instilled confidence that the cooling tubes would consistently meet quality standards
- We successfully produced and shipped thousands of cooling tubes, allowing the EV company to push forward with production while awaiting delivery of the custom-built machinery
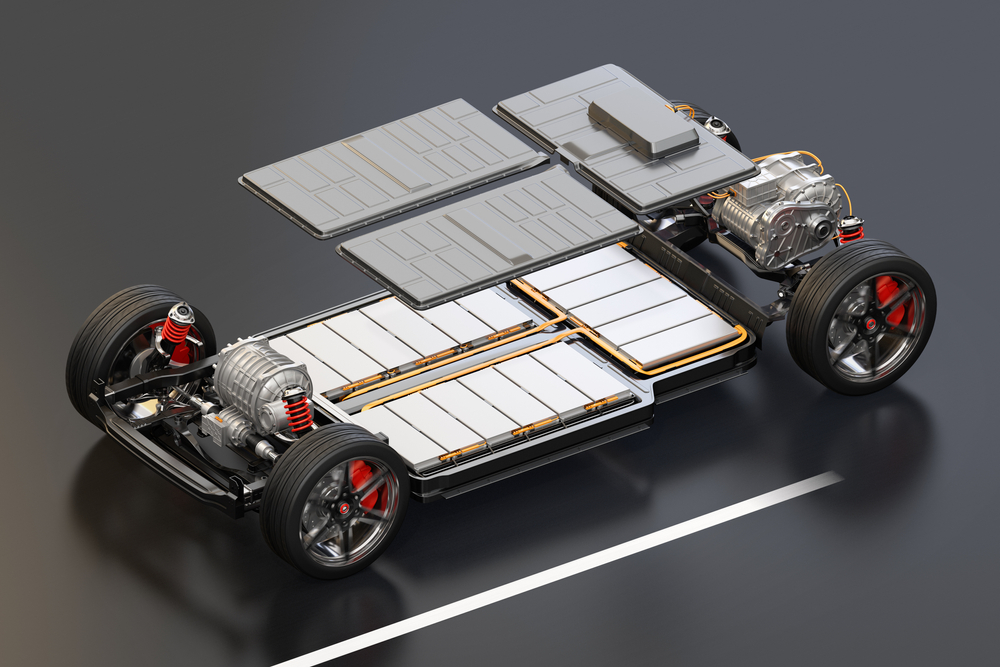